LATEST NEWS
- 01How is photovoltaic power generation integrated into the grid?
- 02How to maintain and maintain the solar panels of photovoltaic power plants?
- 03Do a good job in daily maintenance and build a high-quality photovoltaic power station
- 04About the time calculation method of the battery capacity of the UPS power supply/inverter
- 05Safe use of inverter power
- 06Instructions for use of multi-function inverter
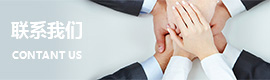
No. 3, Hongli Road, Miaobian Village, Liaobu Town, Dongguan City, Guangdong Province, China
Address:Jinweiyuan Science and Technology Park,No.41,Qingsong Road, LongtianStreet,Pingshan District, Shenzhen City, Guangdong Province
TEL: (+086)15220276096 (+086)13713796273
e-Mail: 635551021@foxmail.com
e-Mail:szhuanyu2004@sina.com
Industry dynamics
HomeIndustry dynamicsDetails
Common faults and causes of lithium battery
Publish: 2022-01-12 15:47:10 View: 392
Summary of abnormal causes of lithium battery, including lithium battery capacity, internal resistance of lithium battery, lithium battery voltage, size, over thickness, open circuit, etc. the capital of batteries has been briefly summarized and shared with you. These abnormal causes will often be encountered in the production process. Netizens are welcome to add~
Common faults and causes of lithium battery are as follows:
1. Low battery capacity
Causes: a. the amount of attached materials is too small; b. There is a large difference in the amount of attached materials on both sides of the pole piece; c. Pole piece fracture; d. Less electrolyte; e. Low electrolyte conductivity; f. The positive and negative plates are not matched properly; g. The porosity of diaphragm is small; h. Adhesive aging → attachment falling off; i. The coil core is too thick (not dried or the electrolyte is not penetrated) J. it is not fully charged when the volume is divided; k. The specific capacity of positive and negative materials is small.
2. High internal resistance of battery
Causes: A. faulty welding between the negative plate and the lug; b. False welding between positive plate and pole lug; c. False welding between positive lug and cap; d. False welding between negative lug and shell; e. The contact internal resistance between rivet and pressing plate is large; f. No conductive agent is added to the positive electrode; g. The electrolyte has no lithium salt; h. The battery has been short circuited; i. The porosity of diaphragm paper is small.
3. Low battery voltage
Causes:
a. Side reaction (electrolyte decomposition; impurities in the positive electrode; water); b. Not formed well (SEI film is not formed safely); c. Leakage of the customer's circuit board (refers to the electric core returned by the customer after processing); d. The customer fails to spot weld as required (the electric core processed by the customer); e. Burrs; f. Micro short circuit; g. The negative electrode produces dendrites.
4. There are several reasons for over thickness:
a. Weld air leakage; b. Electrolyte decomposition; c. UN dried moisture; d. Poor sealing of cap; e. The shell wall is too thick; f. The shell is too thick; g. The coil core is too thick (too much attached material; the pole piece is not compacted; the diaphragm is too thick).
5. Abnormal battery formation
a. Not formed well (SEI film is incomplete and dense); b. Too high baking temperature → adhesive aging → stripping; c. Low specific capacity of negative electrode; d. More positive electrode and less negative electrode; e. Cap leakage and weld leakage; f. The electrolyte decomposes and the conductivity decreases.
6. Battery explosion
a. Fault of the volume dividing cabinet (causing overcharge); b. Diaphragm closure effect is poor; c. Internal short circuit.
7. Battery short circuit
a. Material dust; b. Broken when the shell is installed; c. Ruler scraping (diaphragm paper is too small or not padded); d. Uneven winding; e. Not wrapped properly; f. The diaphragm has holes; g. Burr
8. Battery open circuit.
a) The pole lug and rivet are not welded well, or the effective welding spot area is small;
b) The connecting piece is broken (the connecting piece is too short or welded too low during spot welding with the pole piece)
Common faults and causes of lithium battery are as follows:
1. Low battery capacity
Causes: a. the amount of attached materials is too small; b. There is a large difference in the amount of attached materials on both sides of the pole piece; c. Pole piece fracture; d. Less electrolyte; e. Low electrolyte conductivity; f. The positive and negative plates are not matched properly; g. The porosity of diaphragm is small; h. Adhesive aging → attachment falling off; i. The coil core is too thick (not dried or the electrolyte is not penetrated) J. it is not fully charged when the volume is divided; k. The specific capacity of positive and negative materials is small.
2. High internal resistance of battery
Causes: A. faulty welding between the negative plate and the lug; b. False welding between positive plate and pole lug; c. False welding between positive lug and cap; d. False welding between negative lug and shell; e. The contact internal resistance between rivet and pressing plate is large; f. No conductive agent is added to the positive electrode; g. The electrolyte has no lithium salt; h. The battery has been short circuited; i. The porosity of diaphragm paper is small.
3. Low battery voltage
Causes:
a. Side reaction (electrolyte decomposition; impurities in the positive electrode; water); b. Not formed well (SEI film is not formed safely); c. Leakage of the customer's circuit board (refers to the electric core returned by the customer after processing); d. The customer fails to spot weld as required (the electric core processed by the customer); e. Burrs; f. Micro short circuit; g. The negative electrode produces dendrites.
4. There are several reasons for over thickness:
a. Weld air leakage; b. Electrolyte decomposition; c. UN dried moisture; d. Poor sealing of cap; e. The shell wall is too thick; f. The shell is too thick; g. The coil core is too thick (too much attached material; the pole piece is not compacted; the diaphragm is too thick).
5. Abnormal battery formation
a. Not formed well (SEI film is incomplete and dense); b. Too high baking temperature → adhesive aging → stripping; c. Low specific capacity of negative electrode; d. More positive electrode and less negative electrode; e. Cap leakage and weld leakage; f. The electrolyte decomposes and the conductivity decreases.
6. Battery explosion
a. Fault of the volume dividing cabinet (causing overcharge); b. Diaphragm closure effect is poor; c. Internal short circuit.
7. Battery short circuit
a. Material dust; b. Broken when the shell is installed; c. Ruler scraping (diaphragm paper is too small or not padded); d. Uneven winding; e. Not wrapped properly; f. The diaphragm has holes; g. Burr
8. Battery open circuit.
a) The pole lug and rivet are not welded well, or the effective welding spot area is small;
b) The connecting piece is broken (the connecting piece is too short or welded too low during spot welding with the pole piece)
RECOMMEND
Safe use of inverter power
2022-01-16 20:14:15
Our products have fully considered personal and property safety factors in the production design, but...
Features of power frequency inverter
2022-01-16 19:02:38
1. The power frequency inverter has high performance and strong load capacity. It adopts the most advanced...
Do a good job in daily maintenance and build a high-quality photovoltaic power station
2022-01-16 20:33:17
Photovoltaic power generation is not only green and environmentally friendly, but also in line with the...